Process immersion heaters are essential components in many industrial applications, offering efficient and direct heat transfer to liquids within tanks, reservoirs, or pipelines. They are widely used because of their compact design, high thermal efficiency, and the ability to provide precise temperature control. One of the key factors in using immersion heaters effectively is understanding which industrial fluids they are best suited to heat. Below is an overview of the main categories of fluids commonly heated with process immersion heaters and the factors that make them compatible.
1. Water and Water-Based Solutions
Water is the most commonly heated fluid in both industrial and commercial settings. Immersion heaters are ideal for:
Process water
Boiler feed water
Cooling tower water
CIP (Clean-in-Place) systems
Immersion heaters can maintain a consistent water temperature for cleaning, sterilization, or process operations. When heating water-based solutions that include mild chemicals or detergents, stainless steel sheath materials are typically sufficient.
2. Oils (Mineral and Synthetic)
Industrial oils—such as hydraulic oils, transformer oils, heat transfer fluids, and lubricants—are often heated using specially designed immersion heaters:
Thermal oil heaters can handle high temperatures up to 300°C or more.
High-viscosity oils may require high-density or over-the-side immersion heaters to ensure proper circulation and uniform heating.
The heater sheath must be compatible with the oil type to avoid chemical degradation. Common sheath materials include Incoloy or copper for mineral oils and stainless steel for synthetic oils.
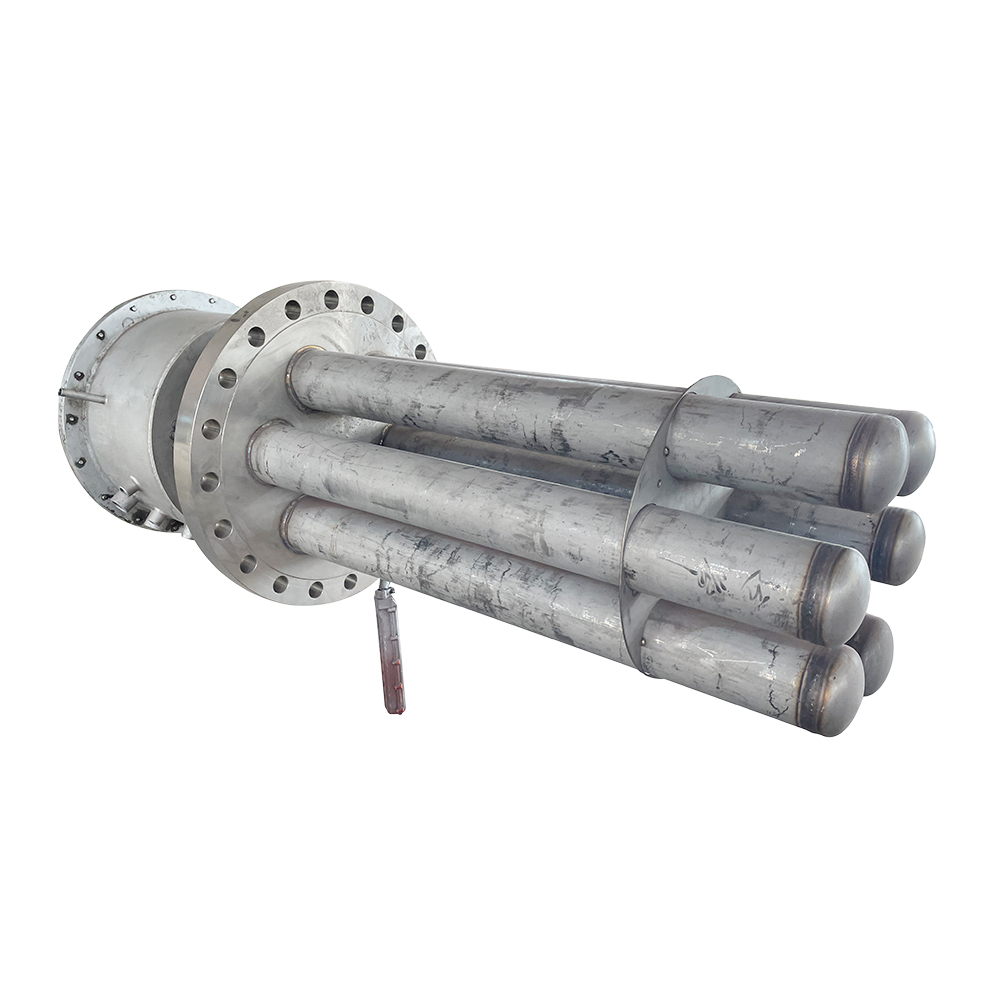
3. Acids and Caustic Solutions
Certain chemical solutions, including acids (e.g., sulfuric, nitric) and alkaline solutions (e.g., sodium hydroxide), require corrosion-resistant materials:
Titanium or quartz sheaths are commonly used to withstand aggressive fluids.
Plastic-coated or Teflon-coated immersion heaters are also an option for sensitive or corrosive applications.
These heaters are typically used in electroplating, chemical processing, and wastewater treatment.
4. Solvents and Flammable Liquids
Solvents like alcohols, ketones, and hydrocarbons can be heated with immersion heaters, but extreme care is needed due to their flammable nature:
Only explosion-proof immersion heaters are suitable.
Temperature controls and safety shut-offs are essential to prevent ignition or overheating.
Applications include paint processing, fuel handling, and pharmaceutical manufacturing.
5. Molten Materials and Waxes
In industries such as candle making, cosmetics, and food processing, low-melting-point materials such as:
Paraffin wax
Vegetable wax
Animal fats
Gels and creams
are often heated using immersion heaters to maintain fluidity. These require low-watt density heaters to prevent scorching or burning of sensitive materials.
6. Glycol Mixtures and Coolants
Ethylene glycol and other antifreeze fluids are widely used in HVAC, cooling systems, and process temperature control loops. Immersion heaters:
Maintain stable operating temperatures
Prevent freezing or viscosity increase in cold conditions
Stainless steel or copper sheaths are typically compatible, depending on the specific formulation of the coolant.
7. Food-Grade Liquids
In the food and beverage industry, immersion heaters are used to heat:
Syrups
Oils
Chocolate
Dairy products
Brewing and fermentation liquids
Heaters used here must meet sanitary standards (e.g., FDA or 3A). Stainless steel is the preferred material for hygiene and corrosion resistance.
Process immersion heaters are highly versatile and can be used to heat a wide range of industrial fluids — from water and oils to chemicals and food products. The key to safe and effective operation lies in selecting the appropriate heater design, sheath material, and control system for the specific fluid. By understanding the compatibility between the heater and the fluid, industries can ensure efficient performance, long service life, and enhanced safety in their operations.