Electric heating elements are devices that convert electrical energy into heat through the process of resistive (or Joule) heating. This technology is foundational in both household appliances and industrial systems, providing efficient and controllable heat sources for a wide range of applications. Whether you're using a toaster, an electric stove, or an industrial furnace, chances are you're benefiting from some form of electric heating element.
How Do Electric Heating Elements Work?
The basic principle behind electric heating elements is Joule heating, which occurs when an electric current passes through a material with electrical resistance. The resistance impedes the flow of current and causes energy to be released in the form of heat. This heat is then transferred to the surrounding environment, either directly or via a medium such as air, water, or metal.
The amount of heat generated depends on the voltage applied, the current flowing, and the resistance of the heating material. This simplicity makes electric heating elements reliable, durable, and easy to control with modern thermostats and sensors.
Types of Electric Heating Elements
Electric heating elements come in various forms, each tailored to specific applications. Below are the most common types:
1. Metallic Heating Elements
These are the most widely used type of heating elements and are typically made from metal alloys with high resistance. Common materials include:
Nichrome (Nickel-Chromium): Perhaps the most common material, nichrome offers high resistance and excellent heat tolerance, making it ideal for household appliances like hair dryers, toasters, and ovens.
Kanthal (Iron-Chromium-Aluminum): Known for its high-temperature performance and longevity, Kanthal is widely used in industrial furnaces and kilns.
Copper-Nickel Alloys: Used in low-temperature applications such as heating cables and underfloor heating systems.
Applications: Water heaters, ovens, irons, hair dryers, air heaters, and more.
2. Ceramic Heating Elements
Ceramic heating elements consist of ceramic materials that are either embedded with heating wires or inherently resistive. These elements are known for providing even and stable heat distribution and are often used when controlled or localized heating is essential.
Types include:
PTC (Positive Temperature Coefficient) ceramics: These self-regulate their temperature, making them safe and energy-efficient.
Infrared ceramic elements: These emit infrared radiation for applications like space heating or industrial drying.
Applications: Space heaters, industrial dryers, soldering equipment, and medical devices.
3. Tubular Heating Elements
Tubular heating elements are versatile and durable, consisting of a resistive coil encased in a metal tube (usually stainless steel or Incoloy) and insulated with magnesium oxide powder. They can be bent into different shapes to fit specific designs and heating zones.
Applications: Electric ovens, water heaters, boilers, industrial tanks, and more.
4. Mica Heating Elements
These elements use mica sheets to support resistive heating wires. The mica provides insulation and structural support while allowing good thermal conductivity and electrical isolation.
Advantages: Fast heat-up times and compact form factors.
Applications: Toasters, hair straighteners, heating pads, and some medical devices.
5. Quartz Heating Elements
Quartz elements are tubular heaters with a nichrome wire coil inside a quartz glass tube. These are often used in radiant heaters where quick heat-up and infrared emission are desired.
Applications: Space heaters, food warmers, and industrial drying equipment.
6. Polymer Heating Elements
These elements use conductive polymers instead of metals. Their primary advantage lies in their flexibility and uniform heating. Many are self-regulating and highly efficient.
Applications: Heated clothing, seat heaters in vehicles, and flexible heating mats.
7. Cartridge Heating Elements
Cartridge heaters are cylindrical and inserted into drilled holes in metal parts. They are capable of delivering concentrated heat at high temperatures in a small area.
Applications: Injection molding machines, packaging equipment, hot stamping, and die heating.
Choosing the Right Heating Element
The selection of an electric heating element depends on several key factors:
Temperature requirements: High-temperature applications (e.g., furnaces) need robust materials like Kanthal or Incoloy.
Environment: Exposure to moisture, chemicals, or physical abrasion can influence material choice.
Heating method: Whether conduction, convection, or radiation is required affects the design.
Form factor: Shape and installation method may determine whether a tubular, cartridge, or flexible element is suitable.
Energy efficiency and safety: Especially important in consumer and medical products.
Electric heating elements are fundamental components that power countless everyday and industrial heating solutions. Their ability to deliver precise, efficient, and reliable heat has led to a wide variety of types and designs to suit nearly any application. From nichrome coils in your toaster to sophisticated ceramic elements in medical equipment, these technologies play a silent but critical role in modern life.
As innovations in materials science and energy efficiency continue, electric heating elements are becoming even more capable—supporting everything from renewable energy storage systems to smart heating in electric vehicles and IoT-enabled homes.
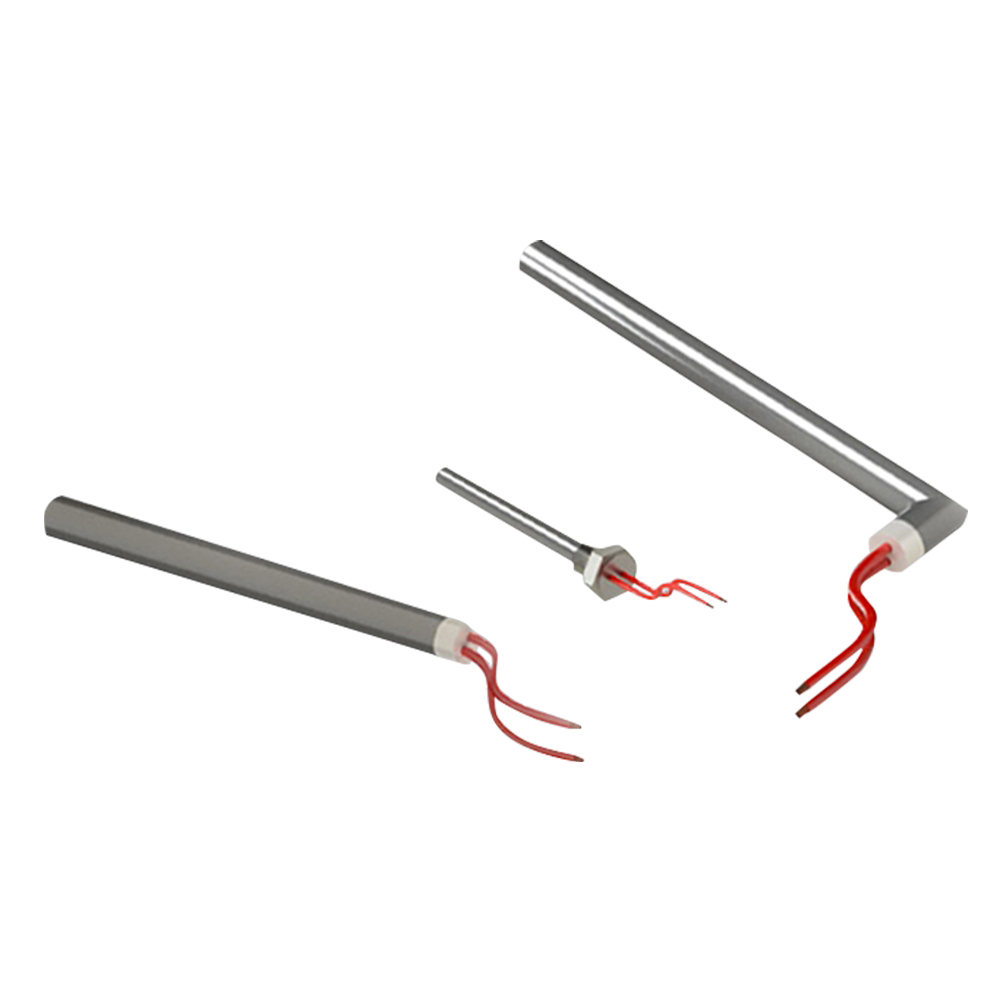